小ロット&多品種組立工場の構内部品・製品の流れ改善
現場改善研修
- レイアウト改善
流れ改善の決め手!構想力を高める研修
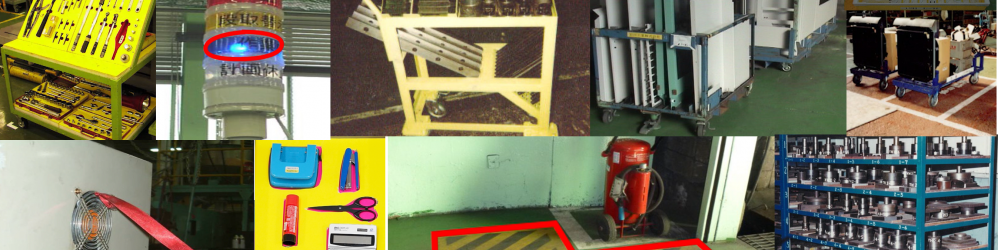
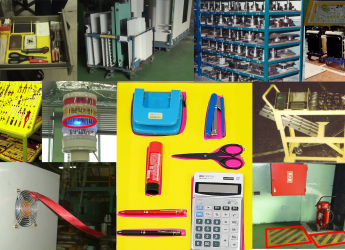
対象・難易度
新人・若手 | リーダークラス | 管理者クラス | 経営者・役員 |
---|---|---|---|
◯ | ◎ | ◯ |
セミナー内容
-
工場内の動線改善は、構想力と設計思想が決め手です。従来の2次元的発想ではうまくいかなかったことも、立体+時間も加えた4次元的という新しい発想を持つことで成功することができます。今までになかった発想の構内物流改善を紹介します。ぜひご参加ください。
- ◆ 1. 生産性向上の考え方
-
(1) 生産革新の目的は、原価低減と価値向上の2つ
(2) 各工程を最適化するIE的発想だけでは限界がある。各工程を連結し全体最適を目指す!
- ◆ 2. 工場レイアウト成功の条件とは?
-
(1) 設計思想のないレイアウト計画は失敗する
(2) 4次元的発想(立体+時間)と現場主義で考える
(3) まず工場のあるべき姿をデザインする
(4) 工程設計から生産システム変更を検討する
(5) 品質と納期優先で生産性向上とコストダウンを狙う
- ◆ 3. 工場の動線改善はこう進める
-
(1) 長く不安定な工程は、密度の高いラインに再編する
(2) 幹線道路の設定と水すまし活用で生産性向上
(3) コンペ方式で現場の知恵を盛り込む
(4) 段ボールを使って実際に人もモノも動かしてみる方式(ビデオ、写真紹介)
(5) 仕掛を大幅に減らすレイアウト改善の進め方
- ◆ 4. ライン改善の具体的な進め方
-
(1) 完成品までの工程を分解して現状の課題を知る
(2) 各工程のネック(品質・作業性・工数など)を把握する
(3) 「魚の骨図」によるライン改善の方法
(4) 段ボールや人を使ってのすぐできるシミュレーションの進め方
- ◆ 5. 構内物流の効果的な改善手法 【具体例】
-
(1) 構内物流は競争力に差をつける最後の武器
(2) 水すましが運行しやすいように十分な通路を確保する
(3) ピッキング工程の2ハンド化でミス防止と工数削減する
(4) 現場改善をしてスペースを確保し「改善コーナー」を設置しよう
(5) 「改善コーナー」による改善推進の実践事例、誰でもすぐに改善ができる仕掛け
- ◆ 6. 工場レイアウト改善事例
-
(1) 製造リードタイム短縮で競争力強化できる
(2) レイアウト改善で余剰な仕掛や在庫を削減できる
(3) 品質向上と工数削減で新たな投資ができる
(4) 納期遵守率が向上し、営業部門負担が軽減できる
(5) 職場の活性化と工場のショールーム化が実現できる
セミナー要項
名称 | 小ロット&多品種組立工場の構内部品・製品の流れ改善 |
---|---|
開催場所 | 大阪府工業協会 研修室 |
定員 | 40名 |
価格(税込み) | 26,400円(会員)/31,900円(非会員) |
開催日・開催予定日
2022年8月30日(火) | 午前9:45 ~ 午後4:45 |
ありがとうございます。
こちらのセミナーは終了いたしました。 お問い合わせはこちらから |
---|